Current Process:
Narrow work wheels prevent generating tapers over 4″ requiring multiple setups to generate the shape. Highly skilled technicians are required to ensure proper setup. Upper and lower slides are strapped, preventing the regulating wheel and work rest blade from being adjusted independently. Wheel dressing is applied manually, which leads to inconsistent wheel conditions. Blade sizing is conducted manually leading to variability in setup longevity.
Challenges:
Deliver a process that can grind up to 8″ tapers on guidewires in one pass while maintaining quality and repeatability. Decrease downtime related to setup and complicated changeovers. The process must meet CE Certification standards for operator safety.
Solution
Solution: Glebar TF-9D Micro Grinder with GFS Standalone Feeding System
The TF-9D Micro Grinder features the widest work wheel on the market measuring 8-5/8″ wide. Top and bottom slides can be positioned independently improving positioning accuracy and reducing setup times. The grinding area is enclosed using CE Certified interlock latches to ensure operator safety. Automatically sizes the work rest blade insert for consistent setups. Provides automatic dressing sequences for both the regulating wheel and work wheel that can easily be set by the HMI. Using our GFS Standalone Feeding System we can automate any Glebar or third-party grinding machine to feed, stage, grind, and unload continuously allowing operators to run other machines concurrently.
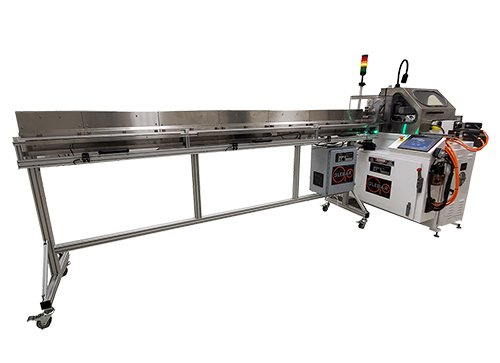
The wider work wheel is capable of grinding shapes up to 7.8″ in a single pass.
Operator friendly touchscreen HMI stores multiple setups for quick retrieval and changeover.
Typical Glebar installations have one operator running three or more machines because of the reliability of the automation and grinder performance.
Paired with a feeding system that automatically picks wires out of a bin and loads them into the machine. During grinding, it stages the next part and unloads the finished part. In testing, a single tapered wire ran at seven seconds, which included loading, grinding, and unloading.
Explore | TF-9DHD Micro Grinding Machines
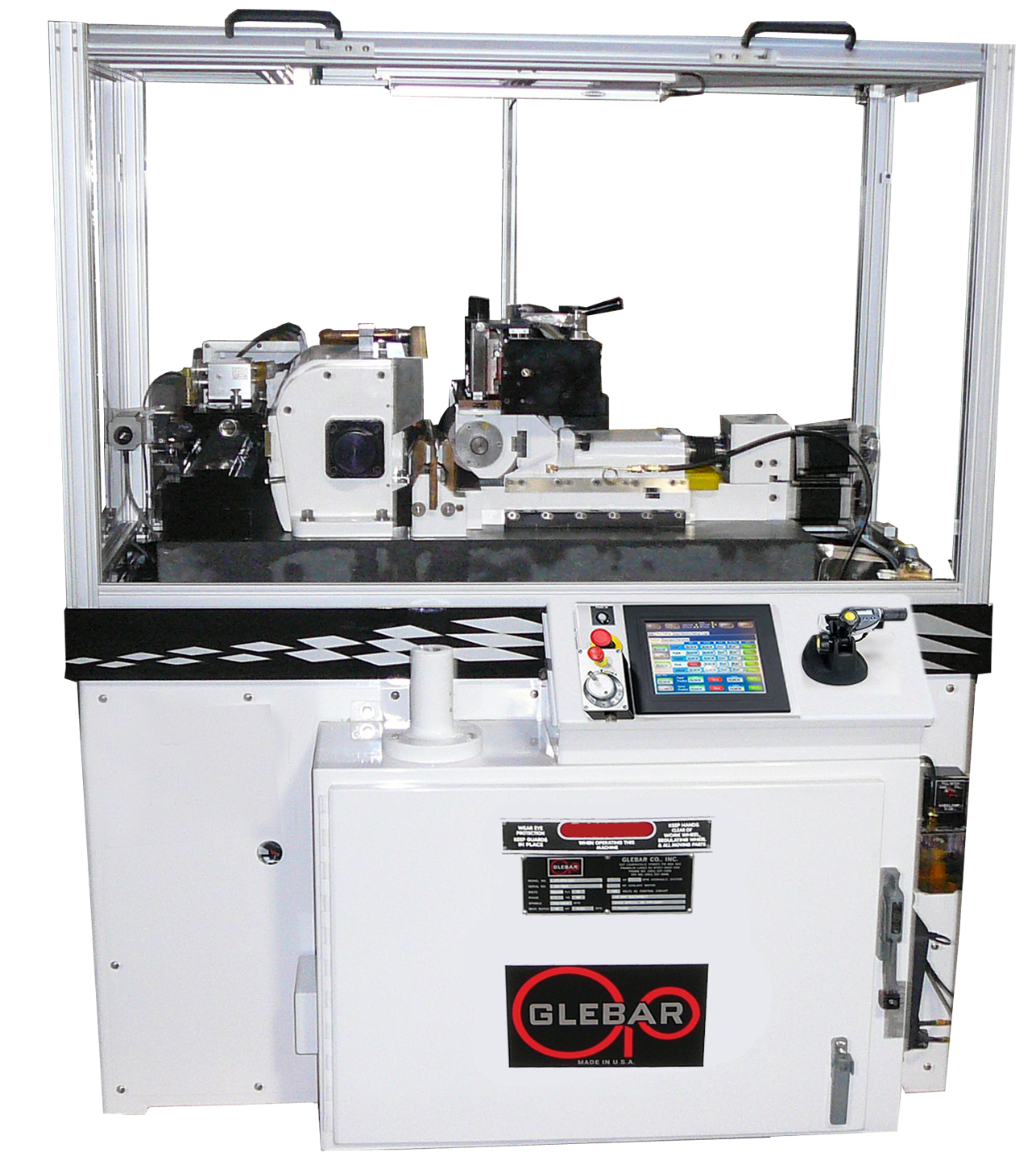
TF-9DHD
The computer controlled TF-9DHD Infeed/Thrufeed Micro Grinder grinds both hard and soft materials, specializing in parts from 1” in diameter down to .002″. The TF-9DHD is utilized to grind catheter, guidewires, pins, bushings, PTFE, plastics, ceramics and other engineered materials.