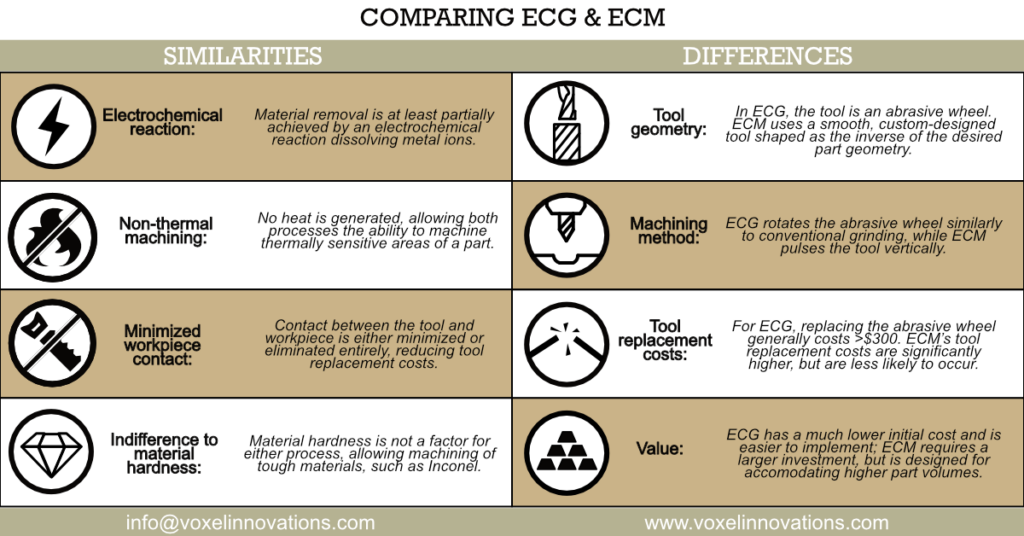
Kirk Gino Abolafia, Technical Sales & Marketing Manager, Voxel Innovations
Elecrochemical grinding (ECG) and electrochemical machining (ECM) are two non-conventional manufacturing processes with some similarities and differences. While both utilize electrochemistry to dissolve metal, the fundamental difference between ECG and ECM lies in their tooling; ECG utilizes a rotating abrasive wheel, while ECM utilizes a tool that is shaped as the inverse of the desired geometry. In this educational article, we’ll compare these similar, but distinctive, technologies and their unique advantages, disadvantages, and applications.
Similarities
The primary similarity between these otherwise distinctive technologies is their usage of electrochemistry as the material removal method. The electrochemical process begins by flushing an electrolytic fluid through a microscopic gap between the tool (cathode) and workpiece (anode). The charged electrolytic fluid forces negative ions to move towards the anode and positive ions to move towards the cathode, thereby dissolving the metal molecules and combining with hydroxyl ions to create metal hydroxides. Depending on the process, these metal hydroxides can then be removed by abrasion or be flushed away by the electrolytic fluid.
Both processes utilize sodium nitrate (NaNO3) as an electrolytic fluid. However, in ECM, other fluids such as concentrated acids are used on rare occasions for enhanced material removal capabilities. The flow, control, and quality of this electrolyte can be critical to the success of both ECG and ECM.
By utilizing electrochemistry rather than friction to remove material, both ECM and ECG are thereby non-thermal processes, allowing them unique advantages. With significantly reduced (ECG) or eliminated (ECM) contact between the tool and workpiece, the tool life in both processes is significantly prolonged. This also provides both processes a high level of repeatability; ECG and ECM can machine many parts without replacing the tool or forgoing accuracy. Another advantage of the non-thermal nature of the processes is their ability to finish surfaces with no resulting burrs, cracks, or thermal distortions, allowing them to machine thermally sensitive areas (such as thin walls).
In addition, electrochemical processes are only concerned with the conductive and electrochemically reactive nature of the material, rather than its hardness; ECM and ECG can machine/finish Inconel at a similar rate to copper. This indifference to material hardness is a driving reason these technologies are often used on temperature-resistant superalloy components for the aerospace industry, for example Inconel turbine vanes.
Compared to conventional machining processes, ECM and ECG are generally faster at removing material, especially with tough-to-machine materials. Faster removal rates, combined with a significant reduction in tool replacement costs allow these processes to have the most significant advantages on medium-to-high volume projects.
Differences
The primary difference between ECM and ECG is the nature and application of the tool (cathode). In ECG, the cathode is an abrasive wheel which is rotated at high speeds and moved toward the workpiece surface. The abrasive wheel in ECG contacts the workpiece, albeit significantly less than a conventional grinding process. While a significant amount of the material removal in ECG can be accredited to the electrochemical process, a portion of material removal can be attributed to the abrasive cutting from the wheel itself, which varies depending on the specific application and cutting parameters. For ECG, a ‘conventional’ tool can be comprised of an aluminum oxide or a silicon carbide, and a ‘super abrasive’ tool can be diamond or CBN in a conductive resin bond.
Conversely, in ECM, the cathode is customized to the part, maintained in close proximity to the workpiece, and does not make any contact with the workpiece. The tool is typically stainless steel or another corrosion-resistant metal alloy and may be manufactured via a variety of manufacturing methods including CNC machining, EDM, additive manufacturing, etc.
ECM is entirely reliant on the electrochemical process to remove material but may apply vibration or motion to the cathode tool to aid in flushing the electrolyte.
Modifying the voltage in each process is a crucial variable for engineers to consider. However, this voltage is generally different depending on the process. In ECG, voltage can range anywhere from 1 to 20 volts, but is typically around 7-12 volts. ECM, however, may require a higher voltage, from 6 to 40 volts or more. In addition, advanced versions of ECM may employ a pulsed voltage waveform (sometimes called pulsed electrochemical machining – PECM).
ECM or ECG?
If you are determining which of these processes would be ideal for manufacturing your parts, ask three questions: that of the material, geometry, and volume.
If the material being machined is non-conductive, such as polymers or ceramics, neither of these processes will be suitable. ECM and ECG can machine any conductive materials including easy-to-machine materials such as copper or aluminum; but these processes will be the most cost-effective when tasked with machining tough materials, such as stainless steels, nickel superalloys, titanium alloys, or (some) refractory metal alloys.
If the material meets this criteria, your next consideration should be the geometry and tolerances of the part. If high surface quality is important to the part, ECG and ECM may be a good fit. Additionally, if the geometry of the part has complexity such as 3D contours, thin walls, or small features (frequent in the aerospace and medical device industries) these processes may be valuable.
If the aforementioned criteria is met, the final (and perhaps most important) question to ask is about the part’s volume.
ECG is a versatile process able to machine parts in low or very high volumes, depending on the application. The universality of the tooling in ECG provides it a significant advantage, allowing manufacturers to quickly switch parts or projects without making more significant modifications. ECG wheels, on average, cost between $150-300, lower than many conventional processes and is considerably lower than ECM’s tooling costs.
The rate of tool wear is significantly dependent on the material, wheel, speed, and tolerance. Glebar refers to the ratio of material removed divided by the amount of wheel consumed as the “G” ratio. For applications such as utilizing a standard aluminum oxide ECG wheel on stainless steel tubing, the G ratio could be about 10 to 15. A higher-quality, super-abrasive wheel could see G ratios as high as 100.
Compare this information with ECM, a process that is more exclusive to high part volumes. As the tool in ECM is fully customized to its respective project, allowing it extremely high repeatability, ECM requires a significantly higher upfront investment to create this tool– about 8 to 10 times higher than simply purchasing an abrasive wheel for ECG. ECM, though, has almost zero tool wear, and with about <12um (.0005in) repeatability, ECM can manufacture a part thousands, or tens of thousands, of times with near-identical features, incurring almost no tool replacement costs. As part volumes increase, the high initial tooling and development costs are increasingly offset, making ECM an ideal process for part volumes in the thousands or tens-of-thousands.
Glebar is an industry expert in electrochemical grinding (ECG) technology. Learn more about our technology, or request a quote on one of our ECG machines here.
Glebar partnered with Voxel Innovations, a pioneer in pulsed electrochemical machining (PECM), to make this article. Learn more about PECM, how it differs from traditional ECM, and its growing applicability in the aerospace and medical device markets here.