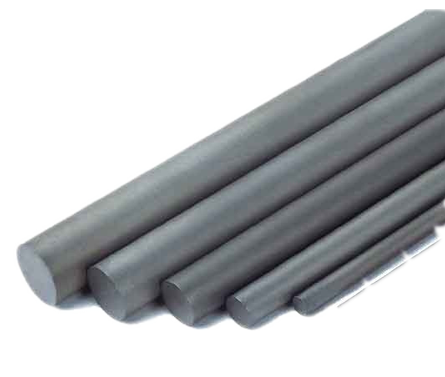
To establish a process whereby pre-sintered carbide drill blanks processed in a hot isostatic press (HIP) can be pre-sized to produce straight rod stock for long blanks. The existing method of manufacture involves sintering the carbide rods in a hot isostatic press then grinding them to size in a hard state before the fluting operation is performed. This procedure requires multiple thrufeed grinding operations which is labor intensive and accelerates wear and tear to the grinding machine and tooling since the hard carbide usually has a non-uniform lumpy surface; furthermore several thrufeed passes are need post-sintering to size the carbide to its final diameter and to achieve the uniform diameter required.

Solution
// Solution: The PG-9x20DHD can infeed grind carbide in the soft or “bisque state” up to 20” wide in one operation. The consistency of chalk, the pre-sintered rod can be sized to near net shape, gently removing the surface imperfections and preparing the rod for the sintering process in one operation. The advantage of this method is that drastically fewer passes are need to be ground post sintering since the material is close to the final shape after being ground on the PG-9X20DHD, carbide dust can be reclaimed, tooling costs for the final thrufeed grind operation is minimized and the overall cost of manufacturing the drill blank is reduced.
The PG-9x20DHD can infeed grind carbide in the soft or “bisque state” up to 20” wide in one operation.
Explore | PG-9X20DHD Form Grinding Machines
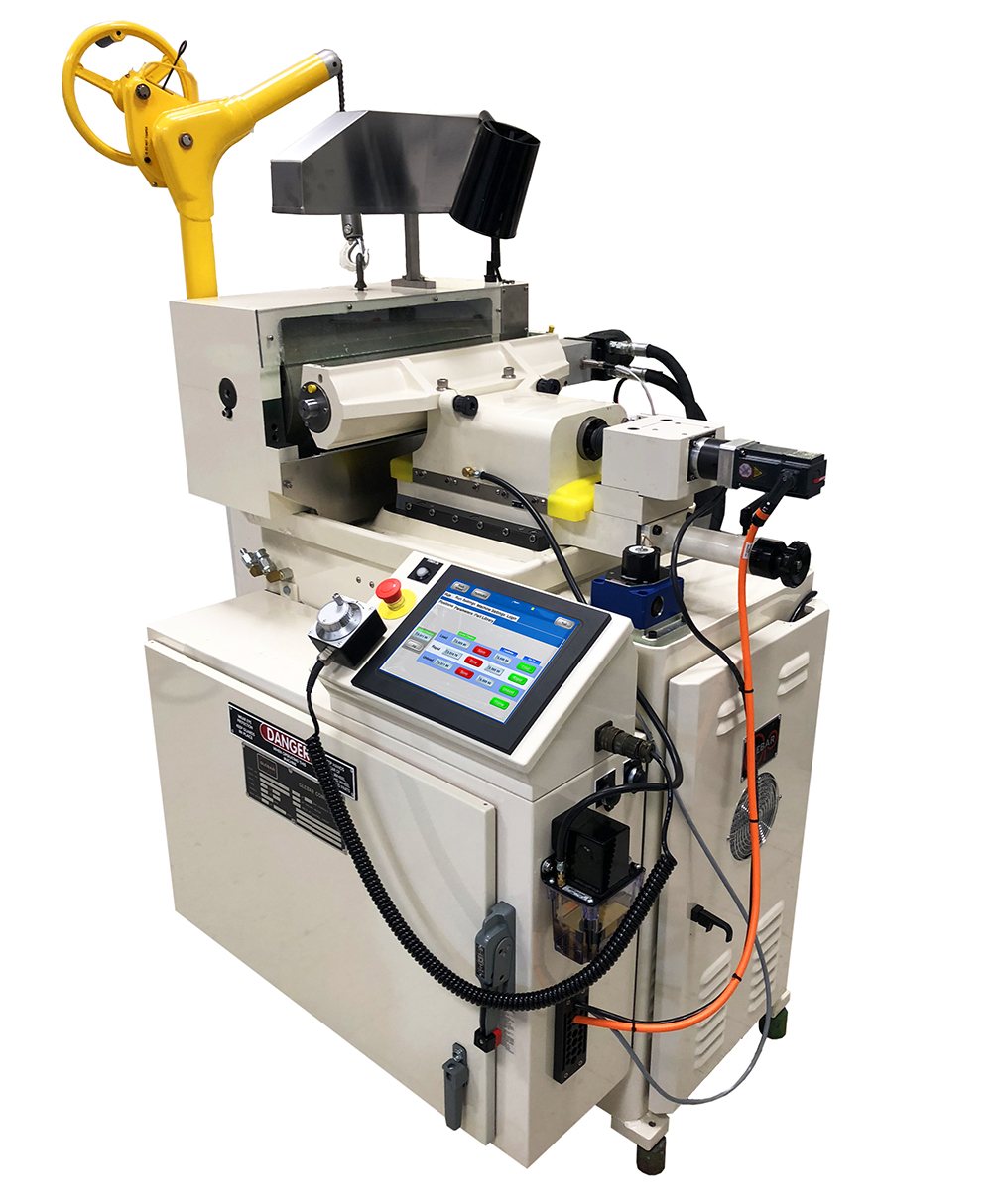
PG-9X20DHD
The PG-9X20DHD form grinding machine was developed to size pre-sintered carbide rods in the pre-fired state. Additional applications include crystal quartz glass boules used to make fiber optics.