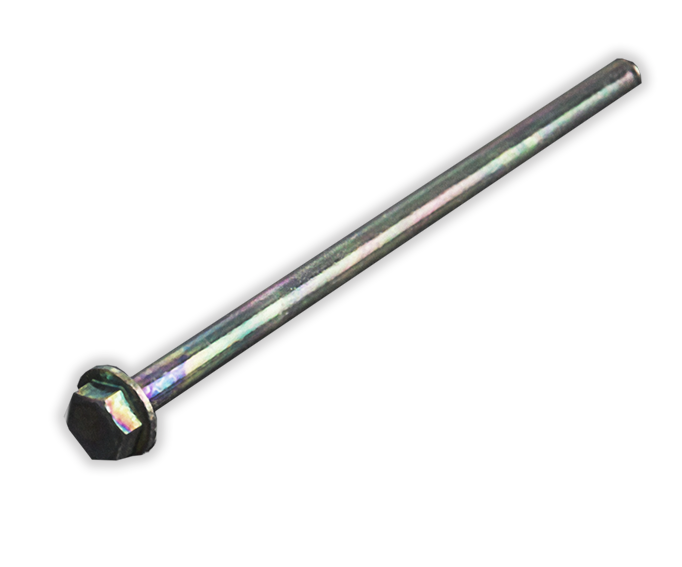
Challenge: A tier one automotive fastener supplier needed to grind bolts for a major automotive company automatically at high volume, with a high degree of precision. The customer’s existing process was outsourced and was running one part at a time, resulting in a higher cost for our customer. In addition, quality and consistency of the components post grind was an issue.
Solution
Glebar provided a one stop shop turnkey solution with gauge feedback and automatic size compensation, running two parts at a time at a rate of approximately 2X the prior production rate. Glebar’s fully enclosed granite-based GT-610 fed by a 32” vibratory bowl feeder, staging automation, and a gantry system was able to load and unload and grind 2 components simultaneously across a 10-1/8”wide twin grip grinding wheel, which made the system ideal for the application. Ground parts are automatically inspected using multiple contact probes to measure taper and feedback diameter to the machine for diameter size control. The solution produced the required high rate of production in a smaller footprint than competing models with one point of support contact for all automation and inspection.
Explore | GT-610 Infeed/Thrufeed Centerless Grinding Machines
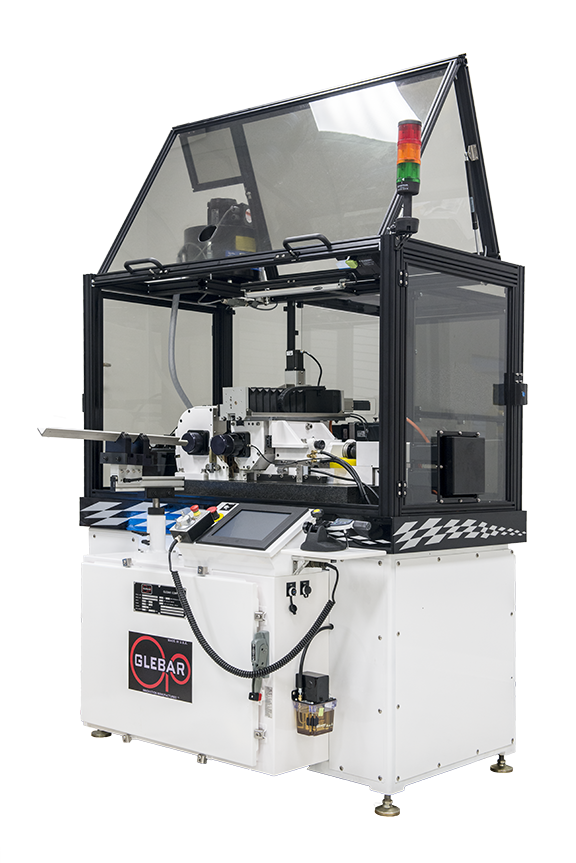
GT-610
The GT-610 Automated Infeed/Thrufeed Centerless Grinding Machine can be custom fitted with automation. This system is the ideal option for when infeed applications do not require a CNC dresser and for the vast majority of thrufeed applications. The GT-610 excels at hard metals and composites, producing carbide blanks, spools, bushings, and engine components such as automotive fasteners and valve lifters. It can also effectively size down metal bars.