Challenge: To thrufeed automatically thru feed grind an automotive component and achieve a 1.2 Rz surface finish
Solution
Using a GT-610 thrufeed machine coupled with a vibratory feeding system that oriented pushrod parts for thrufeed grinding, we were able to use the same automation to cover a wide range of part lengths. The pre-ground 0.098” diameter components had turned diameters so part orientation was critical to insure consistent thrufeed pressure.
We were grinding 0.003” in one pass and achieving a 0.8 Rz surface finish which was significantly better than the required 1.2 Rz requirement.
The advantage on the Glebar was the use of a true twin grip 8-5/8” wide grinding wheel sandwiching multi grit abrasives across the span of the wheel to achieve roundness and straightness of 50 millionths in an automated line. As the parts were light weight, the GT-610 machine tooling is designed to minimize turbulence through the machine while maintaining a tight control grip on the parts to achieve the desired specifications. An offline diameter gage was used to spot check the component diameters and feedback compensation offsets to the machine automatically without stopping the line.
Explore | GT-610 Infeed/Thrufeed Centerless Grinding Machines
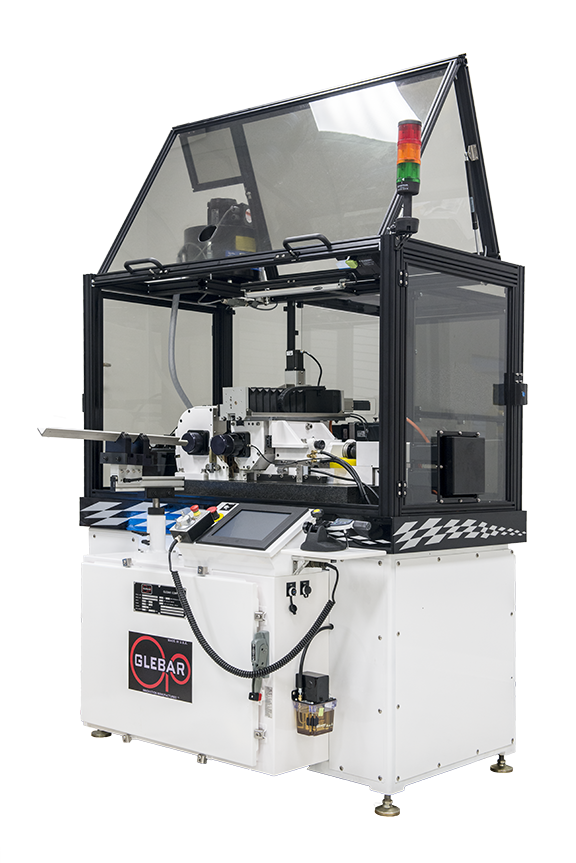
GT-610
The GT-610 Automated Infeed/Thrufeed Centerless Grinding Machine can be custom fitted with automation. This system is the ideal option for when infeed applications do not require a CNC dresser and for the vast majority of thrufeed applications. The GT-610 excels at hard metals and composites, producing carbide blanks, spools, bushings, and engine components such as automotive fasteners and valve lifters. It can also effectively size down metal bars.